Мідь (Cu)
Коли мідь (Cu) розчиняється в алюмінієвих сплавах, механічні властивості вдосконалюються, а продуктивність різання стає кращою. Однак резистентність до корозії зменшується, і гаряче розтріскування схильне. Мідь (Cu) як домішка має однаковий ефект.
Сила та твердість сплаву можуть бути значно збільшені за допомогою вмісту міді (Cu), що перевищує 1,25%. Однак осадження Аль-Ку спричиняє усадку під час лиття штампу з подальшим розширенням, що робить розмір кастингу нестабільним.
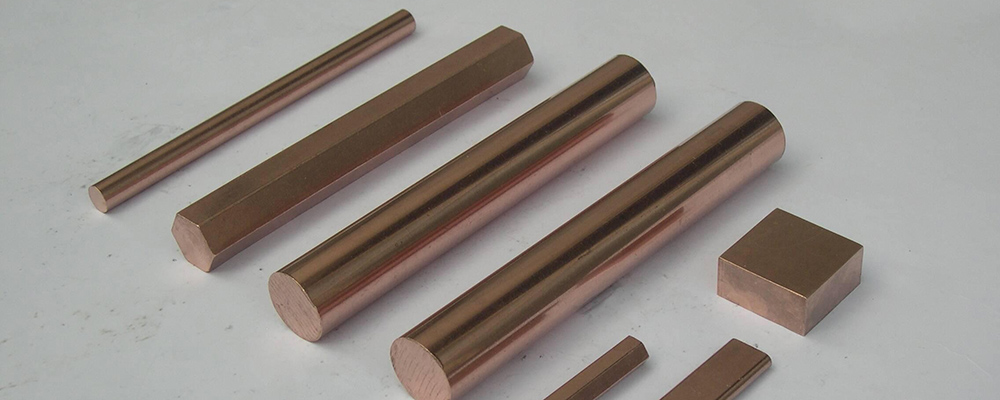
Магній (мг)
Невелика кількість магнію (мг) додається для придушення міжгранулярної корозії. Коли вміст магнію (мг) перевищує визначене значення, плинність погіршується, а теплова міцність та міцність впливу знижуються.
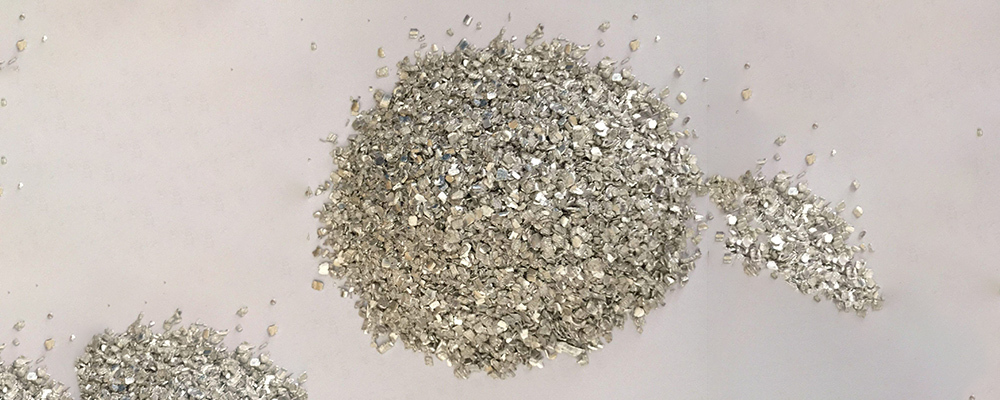
Кремнію (СІ)
Кремнію (СІ) є основним інгредієнтом для підвищення рівня плинності. Найкраща плинність може бути досягнута від евтектичної до гіпертектичної. Однак кремнію (СІ), який кристалізується, має тенденцію до утворення важких точок, що погіршують продуктивність різання. Тому, як правило, заборонено перевищувати евтектичну точку. Крім того, кремній (СІ) може покращити міцність, твердість, твердість, скорочення та міцність при високій температурі, зменшуючи подовження.
Алюміній-магнезієвий сплав магнію (мг) має найкращу резистентність до корозії. Тому ADC5 та ADC6 є стійкими до корозії сплавів. Його діапазон затвердіння дуже великий, тому він має гарячу крихкість, і кастинги схильні до розтріскування, що ускладнює кастинг. Магній (мг) Як домішка в матеріалах аль-Ку-Сі, MG2SI зробить лиття крихкою, тому стандарт, як правило, становить 0,3%.
Залізо (Fe), хоча залізо (Fe) може значно підвищити температуру перекристалізації цинку (Zn) і уповільнити процес перекристалізації, в плавленні, заліза (Fe) надходить від залізних розгинань, труб з гусеником та засобів плавлення, і розчинний у Zinc (Zn). Залізо (Fe), що переноситься алюмінієм (Al), надзвичайно мало, і коли залізо (Fe) перевищує межу розчинності, воно буде кристалізуватися як Feal3. Дефекти, спричинені здебільшого Fe, генерують шлак і поплавок як сполуки Feal3. Кастинг стає крихким, а обробка змінюється. Плинність заліза впливає на гладкість поверхні лиття.
Домішки заліза (Fe) генеруватимуть голкоподібні кристали Feal3. Оскільки штамп швидко охолоджується, осаджені кристали дуже тонкі і не можуть вважатися шкідливими компонентами. Якщо вміст менше 0,7%, це непросто, тому вміст заліза на 0,8-1,0% кращий для штампування. Якщо є велика кількість заліза (Fe), будуть утворені металеві сполуки, утворюючи жорсткі точки. Більше того, коли вміст заліза (Fe) перевищує 1,2%, це зменшить плинність сплаву, пошкодить якість лиття та скоротить термін експлуатації металевих компонентів у обладнанні штампування.
Нікель (NI), як мідь (Cu), існує тенденція до підвищення міцності та твердості на розрив, і він має значний вплив на резистентність до корозії. Іноді нікель (Ni) додається для поліпшення високої температури та тепловідповідачі, але це негативно впливає на корозійну стійкість та теплопровідність.
Марганець (MN) може покращити високотемпературну силу сплавів, що містять мідь (Cu) та кремнію (СІ). Якщо він перевищує певну межу, легко генерувати al-si-fe-p+o {t*t f; x mn четвертинні сполуки, які можуть легко утворювати жорсткі точки та зменшити теплопровідність. Марганець (MN) може запобігти процесу перекристалізації алюмінієвих сплавів, підвищити температуру перекристалізації та значно вдосконалити зерно перекристалізації. Удосконалення зерен перекристалізації в основному пояснюється заважаючим ефектом сполук MNAL6 на зростання зерен перекристалізації. Ще одна функція MNAL6 - розчинення домішувального заліза (Fe) для формування (Fe, Mn) Al6 та зменшення шкідливого впливу заліза. Марганець (MN) є важливим елементом алюмінієвих сплавів і може бути доданий як окремий бінарний сплав Аль-Мн або разом з іншими легуючими елементами. Тому більшість алюмінієвих сплавів містять марганцю (MN).
Цинк (Zn)
Якщо нечистий цинк (Zn) присутній, він буде виявляти високотемпературну крихкість. Однак у поєднанні з ртуті (Hg) для утворення сильних сплавів HGZN2 вона виробляє значний зміцнюючий ефект. JIS передбачає, що вміст нечистого цинку (Zn) повинен бути менше 1,0%, тоді як іноземні стандарти можуть дозволити до 3%. Ця дискусія стосується не цинку (Zn) як компонента сплаву, а скоріше його роль як домішки, яка, як правило, викликає тріщини на кастингу.
Хром (CR)
Хром (CR) утворює інтерметалічні сполуки, такі як (CRFE) AL7 та (CRMN) AL12 в алюмінієві, перешкоджаючи зародженню та зростанню перекристалізації та забезпечують певні зміцнювальні ефекти на сплав. Це також може покращити міцність сплаву та зменшити чутливість до розтріскування стресу. Однак це може підвищити чутливість гасіння.
Титан (Ti)
Навіть невелика кількість титану (Ti) у сплаві може покращити його механічні властивості, але він також може знизити його електропровідність. Критичний вміст титану (Ti) у сплавах серії аль-Ті для затвердіння опадів становить приблизно 0,15%, і його присутність може бути зменшена з додаванням бору.
Свинець (PB), олово (SN) та кадмій (CD)
Кальцій (CA), свинець (PB), олово (SN) та інші домішки можуть існувати в алюмінієвих сплавах. Оскільки ці елементи мають різні точки плавлення та структури, вони утворюють різні сполуки з алюмінієм (AL), що призводить до різного впливу на властивості алюмінієвих сплавів. Кальцій (CA) має дуже низьку тверду розчинність в алюмінієві і утворює сполуки CAAL4 з алюмінієм (AL), що може покращити продуктивність різання алюмінієвих сплавів. Свинець (PB) та TIN (SN)-це метали з низькою картовою точкою з низькою твердою розчинністю в алюмінієві (AL), що може знизити силу сплаву, але покращити його показники різання.
Збільшення вмісту свинцю (PB) може знизити твердість цинку (Zn) та збільшити його розчинність. Однак, якщо будь -який з свинцю (PB), олова (SN) або кадмію (CD) перевищує вказану кількість в алюмінієвому сплаві: цинк, може виникнути корозію. Ця корозія є нерегулярною, виникає через певний період і особливо виражена при високій температурі атмосфери з високою висотою.
Час посади: 09-2023